Comprehending What is Porosity in Welding: Reasons and Solutions
Wiki Article
Porosity in Welding: Identifying Common Issues and Implementing Ideal Practices for Avoidance
Porosity in welding is a pervasive concern that commonly goes unnoticed up until it creates significant troubles with the stability of welds. This common defect can jeopardize the stamina and sturdiness of welded structures, posturing safety and security threats and leading to pricey rework. By understanding the source of porosity and carrying out efficient avoidance strategies, welders can significantly enhance the high quality and reliability of their welds. In this conversation, we will certainly explore the essential factors adding to porosity development, analyze its detrimental effects on weld performance, and discuss the very best methods that can be adopted to lessen porosity incident in welding processes.Usual Sources Of Porosity
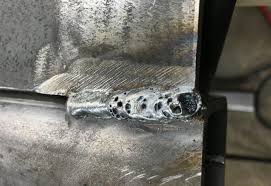
Using unclean or wet filler materials can introduce pollutants right into the weld, contributing to porosity problems. To alleviate these common reasons of porosity, detailed cleansing of base steels, appropriate protecting gas choice, and adherence to optimum welding criteria are essential methods in attaining top quality, porosity-free welds.
Effect of Porosity on Weld High Quality

The existence of porosity in welding can significantly jeopardize the architectural integrity and mechanical residential or commercial properties of bonded joints. Porosity produces voids within the weld metal, deteriorating its general toughness and load-bearing capability. These spaces serve as anxiety concentration points, making the weld extra prone to cracking and failing under used tons. In addition, porosity can minimize the weld's resistance to rust and various other ecological factors, better diminishing its durability and efficiency.
Welds with high porosity degrees tend to show lower impact strength and minimized capacity to warp plastically prior to fracturing. Porosity can impede the weld's ability to successfully transfer pressures, leading to early weld failing and potential safety and security risks in crucial frameworks.
Finest Practices for Porosity Avoidance
To boost the architectural integrity and top quality of welded joints, what specific steps can be implemented to reduce the incident of porosity during the welding procedure? Porosity avoidance in welding is vital to ensure the integrity and strength of the last weld. One reliable method appertains cleansing of the base metal, eliminating any type of contaminants such as corrosion, oil, paint, or dampness that might lead to gas entrapment. Making sure that the welding devices remains in excellent condition, with tidy consumables and ideal gas flow rates, can also considerably decrease porosity. Furthermore, maintaining a steady arc and controlling the welding specifications, such as voltage, present, and take a trip rate, aids produce a regular weld pool that reduces the danger of gas entrapment. Making use of the appropriate welding strategy for the details material being bonded, such as adjusting the welding angle and gun setting, can even more stop porosity. Regular assessment of welds and immediate remediation of any type of issues recognized during the welding procedure are essential practices to protect against porosity and create high-quality welds.Value of Appropriate Welding Techniques
Executing appropriate welding strategies is vital in ensuring special info the architectural stability and top quality of welded joints, building upon the foundation of reliable porosity avoidance measures. Welding methods straight influence the total stamina and sturdiness of the welded structure. One crucial facet of proper welding strategies is keeping the proper heat input. Too much warm can result in enhanced porosity because of the entrapment of gases in the weld pool. Alternatively, insufficient warm might result in incomplete combination, developing possible weak factors in the joint. In a knockout post addition, utilizing the appropriate welding criteria, such as voltage, existing, and travel speed, is critical for attaining audio welds with minimal porosity.Moreover, the choice of welding procedure, whether it be MIG, TIG, or stick welding, should straighten with the details needs of the project to ensure optimum outcomes. Proper cleaning and prep work of the base metal, along with selecting the ideal filler material, are also crucial parts of competent welding techniques. By adhering to these ideal methods, welders can lessen the risk of porosity formation and create top quality, structurally audio welds.
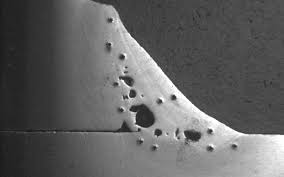
Checking and Top Quality Control Steps
Checking procedures are essential to detect and protect against porosity in welding, making certain the toughness and toughness of the final item. Non-destructive testing approaches such as ultrasonic testing, radiographic testing, and aesthetic assessment are commonly utilized to identify possible problems like porosity.Post-weld assessments, on the various other hand, examine the last weld for any type of flaws, including porosity, and confirm that it satisfies defined standards. Executing a thorough high quality control strategy that consists of thorough screening procedures and assessments is paramount to reducing porosity click here to read issues and making certain the overall high quality of welded joints.
Verdict
In conclusion, porosity in welding can be a common problem that influences the high quality of welds. By identifying the usual reasons for porosity and carrying out finest practices for avoidance, such as proper welding strategies and screening measures, welders can make sure high top quality and trusted welds. It is necessary to prioritize prevention approaches to decrease the event of porosity and keep the stability of welded frameworks.Report this wiki page